Heat exchanger
leakage diagnostics
Detection of early hairline cracks and hole corrosion on assembled plate heat exchanger
Heat exchanger leakage diagnostics
Detection of early hairline cracks and hole corrosion on assembled plate heat exchanger
What is heat exchanger leakage diagnostics without disassembly?
Sometimes a crack or hole on a plate heat exchanger will cause the two liquids to flow together. The loss of production due to the removal of the heat exchanger can result in a serious material loss. Our leakage diagnostics service offers a precise, cost-effective solution.
Heat exchanger leakage diagnostics is a special test method for which the plate heat exchanger does not need to be dismantled or removed, as it is carried out in an assembled state on site.
This test, carried out using special equipment, reliably detects whether there are cracks or holes in the heat exchanger plates.
Hairline cracks and holes can also be detected
After draining the liquids, one side is filled with a forming gas containing a safe concentration of hydrogen.
On the other side, the hydrogen concentration is measured with a high-sensitivity gas analyser (instrument sensitivity 0.5ppm).
The small size and agility of the hydrogen molecules and the high sensitivity of the instrument ensure that incipient hairline cracking or pitting corrosion can be detected that is not detectable at that stage by other methods (e.g. aqueous pressure test, penetration test, etc.).
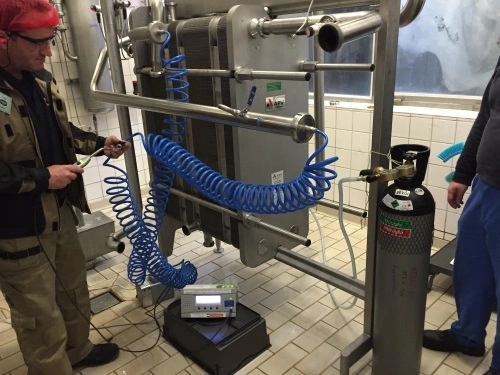
On-site leakage diagnostics
Why carry out leakage diagnostics?
Early detection of plate wear
Maintenance becomes more predictable
With heat exchanger diagnostics to avoid infections in the food industry and cross-contamination in the fine chemicals industry
The traditional theory that the only way to prevent contamination/infection from entering the pasteurised product in pasteurisers is to apply more pressure on the pasteurised side in all cases, is not supported by recent researches.
Renowned professional studies have confirmed that mass transfer can occur in the case of cracks/holes even against a positive pressure gradient due to osmotic pressure (Reference: Raimund Kalinowski, Brauindustrie 08/2007).
By regular inspection and maintenance of the plate heat exchanger, these contaminations can be avoided in the food industry.
In the fine chemical industry, cross-contamination can also be caused by small cracks and holes, which can also be avoided and prevented by this method.
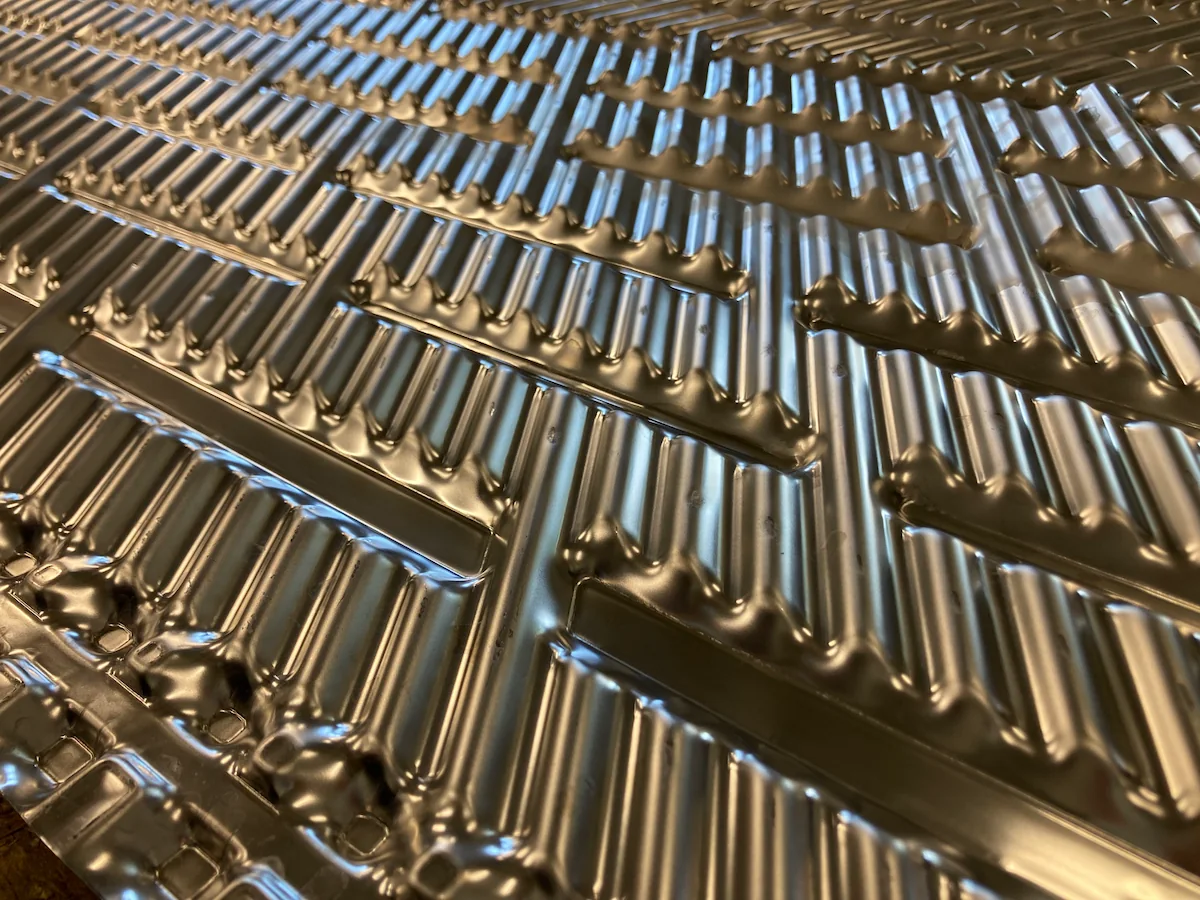
REQUEST A QUOTE
With 25+ years of experience, our professionals are at your service with the highest level of expertise and know-how.